Detailed knowledge of the structure of spray dryer
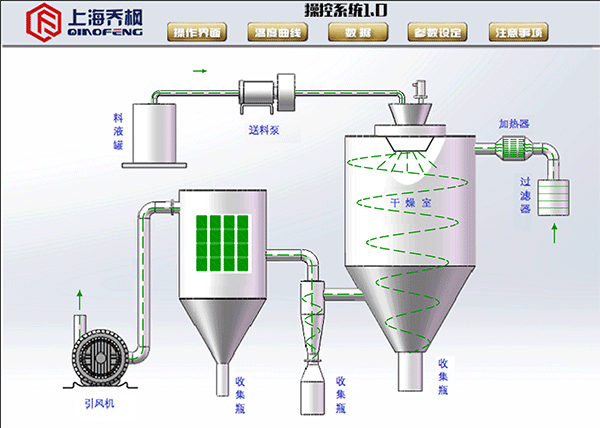
(Structure chart of spray dryer)
For different needs, spray dryer also has many classification methods, such as gas and liquid flow, divided into parallel flow (downstream), countercurrent and mixed flow. According to the installation of atomizer, there are upper and lower spray type and lower spray type; according to the system, there are open type, part circulation type and closed type. As we all know, there are many kinds of fog separator for spray drying, but according to their atomization basis, atomizer is divided into three types: centrifugal, pressure and airflow. Traditionally, spray dryer is classified according to atomization mode, that is, according to the structure of atomizer. Spray drying is divided into three types: rotary type (centrifugal type), pressure type (mechanical type) and airflow type. It has been nearly twenty years since the spray dryer was used in large quantities. The early industrialization of Zui in China should be airflow spray dryer. However, with the successful development of centrifugal and pressure spray dryer, the shortcoming of energy consumption of airflow spray dryer is obvious (nebulizer consumption of energy is 4~8 times of the other two). In recent years, Zui has been gradually replaced by two other models in large-scale industrial production, but it is still in use due to the special needs of the pharmaceutical industry. The high speed nebulizer of centrifugal spray dryer is the key equipment. The problem of amplification has high technical requirements. At present, our country not only has the capability of producing centrifugal atomizer of airflow, machinery and electromechanical integration, but also can achieve the hourly capacity of 45t water. There are professional atomizer factories in Hangzhou, Xining, Wuxi and Jingjiang. At present, the centrifugal spray dryer has formed a serialized model from hourly capacity to several tens of tons per hour. Production and manufacturing technology is basically mature. The product of pressure spray dryer is particulate, and has been widely applied in synthetic detergent, dyestuff, water treatment agent and so on. At present, the pressure sprayer dryer designed and manufactured by our country can reach 8m in diameter, up to 50 meters, and evaporation capacity is up to several tons of water per hour.
At present, in many drying equipment, spray dryer is one of the drier with higher output value, each set from several hundred thousand to several million. In Wenzhou, Shanghai, Wuxi, Jiangyin, Xining and other places, there are many professional manufacturers of spray dryer, providing hundreds of sets of spray drying equipment to customers every year. From the research point of view, the research content of spray drying technology is the first in every academic conference of the national dry meeting. The theoretical imperfections and wide application have attracted the attention of a large number of researchers. The centrifugal atomizer developed by Niro Company in Denmark is famous for its high precision, high speed and energy saving. It can not only achieve uniform and controllable particle size atomization, but also has a large single processing capacity of 200 t/h. This provides a powerful atomization for the development of large spray dryer. Anhydro's centrifugal atomizer uses belt drive and improves the lubrication system, and achieves good results. These achievements are one of the important reasons for the rapid growth of centrifugal atomization applications. China has developed dozens of tons of evaporation per hour, which still lags far behind the level of foreign countries. Spray dryer is a drying equipment for treating solution, suspension or slurry material. It uses spray method to make the material become droplet dispersed in hot air, and the material is in contact with the hot air in the way of parallel flow, countercurrent or mixed flow, so that the moisture evaporates quickly and achieves the purpose of drying. With this drying method, unit operations such as concentration, filtration and crushing can be omitted, and granular products of 30-500 um can be obtained. And the drying time is very short, the general drying time is 5 ~ 30 s. It is suitable for the drying of highly thermal sensitive materials and dispersible materials in the process of concentration of material and liquid. The product has good fluidity and instant solubility. In the spray dryer, the gas solid two phase contact area is large, but the gas solid two phase is dilute phase flow. Therefore, the volume heat transfer coefficient is small, generally 20~100kcal/m3? H? C, the inlet temperature of hot air is 260~500 260~500 at the co current operation, and the operating temperature is about 200~300 C. Industrial scale spray dryer, the thermal efficiency is generally 30~50%. Foreign spray drying with waste heat recovery, thermal efficiency can reach 70%, but this device is only greater than 100kg (water) /h production capacity is of economic significance. The basic process of spray drying is as follows: the slurry is dispersed through a nebulizer and droplets are dispersed in the hot gas stream. The air is heated by air blower into the air heater, then enters the spray dryer and DRIs and DRIs with the droplet. Part of the product falls to the bottom of the tower. Part of the product is inhaled by a first-stage induced draft fan into a first-stage cyclone separator. After separation, the exhaust gas is exhausted. The products at the bottom of the tower and those collected by the cyclone separator are extracted by the secondary exhaust fan and packed after the separation by the secondary cyclone separator. Spray drying products are fine particles. In order to meet the requirements of environmental protection, it is not enough to spray the drying system to separate products and purify the exhaust gas only by cyclone separator. If the dust content in the tail gas is less than 50 mg/Nm3 or wet scrubber is used, the dust content in the tail gas can be reduced to 15-35 mg/Nm3.(two) progress in spray drying technology Spray drying is widely used in chemical industry, light industry, food industry and so on because it can be directly obtained from solution or suspension system with homogeneous powder products. In chemical industry, Zui is widely used in dyestuff industry. After years of efforts of engineers and technicians, spray drying technology has been relatively mature, and the determination of tower size also has a successful calculation method. The nebulizer used is still three kinds of pressure, centrifugal and airflow, but in recent years the application of centrifugal spray dryer is on the rise. For real solution spray drying, it is worth noting that the temperature of the drying medium required by different hydrophilic solutes is different. For inorganic salts with strong hydrophilicity, evaporation and dehydration of aqueous solution are mainly carried out at the boiling point of the solution, and it is difficult to operate the outlet gas temperature below 130 C. Although there is a clear gap between China and foreign countries, the manufacturing and operation level of spray drying equipment has also been greatly improved. In recent 20 years, the improvement and innovation of spray drying technology and equipment are mainly in the following aspects:(1) Solving the problem of wall sticking Sticking phenomenon is still a prominent problem that hinders the normal operation of spray dryer. Generally speaking, increasing the diameter can reduce the wall sticking, but it is obviously not economical to use very large equipment diameter for this purpose. Foreign experts have studied the problem of sticking and caking in drying process. They think that the main macro factor causing sticking is wall temperature. The solution to orange juice spray drying is to cool the tower wall below the temperature of the dry product and add a drying aid in the feed liquid. Masters proposed three possible ways to prevent wall sticking: Firstly, a clipped drying tower is adopted, in which air is used to cool the wall temperature to keep below 50 C. Flat bottom tower is suitable for materials with strong cohesion. (2) The secondary air cooling tower wall is introduced tangentially through the swirling section of the tower wall; (3) Install an air broom consisting of a row of nozzles near the wall of the tower and make it rotate slowly along the wall. Obviously, the basic effect of these measures is the same, that is, cooling tower wall. These methods have been applied in the drying of Chinese herbal extracts and have certain effects. In addition, the polishing of the inner wall of the tower can also reduce the stickiness of the wall.(2) Improving the physical properties of products With the development of science and technology and the improvement of living standards, the physical properties of spray drying products are increasingly demanding. For example, some require bulk density to be very high (> 1.0) or very small (< 0.6), while some rehydrated powders such as food and Chinese medicine granules often require instant solubility. Generally speaking, products with different bulk densities can be produced by changing atomization dispersion and operating conditions to control drying rate, but the range of change is limited. In improving physical properties, it is worth mentioning that foam spray drying is about to first feed liquid before foaming, then spray drying. The method Zui was first proposed to improve thermal efficiency, and later used to adjust the physical properties of products. It has been proved that the products such as milk powder produced by foam spray drying are large, porous, porous and rough, and have good instant solubility. Since the 1980s, this technology has been used in industrial production.(3) Development of multi-objective processes The combination of spray drying and other unit processes has been successfully developed and applied in two main categories. One is spray drying reaction process. One of the typical examples is the spray drying polymerization one step process to prepare sodium tripolyphosphate. But from the point of view of energy consumption, it is not a successful example. The energy consumption per unit product is higher than that of two-step method. It seems that to achieve this combination economically, one of the necessary conditions is that the material temperature required for drying and reaction is basically the same or similar. Another type of multi-target process that has been developed and applied more successfully is spray granulation drying, that is, spray or coating suspension of liquid or suspension on fine-grained material and granulating. Particle drying is usually carried out in fluidized beds (some use drums). Solution atomizers can be placed inside or above the granular bed according to the particle size requirements. Spray granulation drying technology has been used and applied earlier, and much basic research has been done. As there are many products, such as fertilizers, dyes and so on, making granules is more conducive to storage, transportation and use, and interest in these technologies has been growing over the years. According to the available technology, the design and operation of the device with the diameter of bed less than 1 m are easy to solve, but for the large device, it seems that the problem of enlargement needs further study.(4) Development of combined drying equipment It can be directly dried from liquid to powder, which is the Zui advantage of spray drying. However, spray drying is also a major drawback of Zui because of its low thermal efficiency, large volume, low production capacity and high investment. In recent years, Chinese and foreign drying experts have done a lot of research on multistage combined drying with spray drying. It dries the liquid into solid and then enters the next dryer for further drying. In this way, the shortcomings of spray dryer are overcome, and the situation in this area will be introduced in the following contents.(three) brief introduction of three spray drying devices1. airflow spray dryer Because the power (compressed air) consumption of the airflow atomizer is larger than that of the pressure atomizer and the rotary atomizer, it is generally used for drying small batches of products. Air-flow nozzle can easily produce very fine or large droplets. Compressed air or superheated steam with pressure of 0.2-0.5 Mpa is used in the atomizer to spray liquid into droplets through the nozzle. It is an ideal drying equipment for laboratories or intermediate factories. For the atomization of non-Newtonian liquid, the airflow mode is superior to other types. Three-fluid atomizer is very effective for atomizing paste or filter cake with high viscosity. Spray drying in China begins with airflow, and has accumulated rich experience in the design, manufacture and operation of airflow nozzles.2. Pressure fog dryer Due to the increasing demand for granular products such as instant milk powder, hollow particle dye, spherical catalyst, white carbon black and granular ferrite, the pressure spray drying device has also developed. Our country has designed and manufactured several kinds of pressure spray drying equipment of various specifications, and now we have mastered the design, manufacture and operation technology of this type. Pressure atomization is a high-pressure pump to pressurize the material to 2-20 Mpa, and then send it into the atomizer to spray the material into a spray. The amount of spray can reach several tons to ten tons per hour, which can meet the needs of various industries. In industrial production, several or even a dozen nozzles can be installed in a tower, which can keep in full conformity with the experimental conditions, and there is basically no enlargement problem.3. centrifugal spray dryer The centrifugal spray dryer relies on the centrifugal force generated by the high-speed rotation of the atomizing disk. The centrifugal atomizer has a rotary speed of 4000~20000r/min and Zui up to 50000r/min. The sprayer of the nebulizer is short and thick (L/D=1.5~2, L is Takeo and D is the tower diameter). The circumferential speed of the rotating disk is the main parameter of atomizing quality, and the circumferential speed of the design is 90~160m/s. In order to resist abrasion, the atomizing disk is lined with wear-resistant materials, such as ceramics and cemented carbide, in addition to directly forming circular holes and rectangular channels. For industrial spray drying with large spray volume (from several tons to 100 tons per hour), such as flue gas desulfurization of thermal power plants, rotary atomizer can be used, usually with only one nebulizer.(four) spray drying industrial products1. Polymers and Resin Products Acrylonitrile butadiene resin, acrylonitrile butadiene styrene resin, melamine formaldehyde resin, polyformaldehyde, phenol formaldehyde resin, polyacrylic acid ester, polyacrylonitrile, polycarbonate, polyethylene, polyaldehyde, polypropylene, polystyrene, polyvinyl acetal, polyvinyl alcohol butyrate, polyvinyl acetal, polyvinyl chloride emulsion, polyvinyl chloride suspension Floating colloid, impregnated cellulose, styrene acrylonitrile resin, styrene butadiene resin, urea formaldehyde resin, polyvinyl chloride acetate, polyvinyl alcohol.2. Drying of Catalysts Such as acrylonitrile catalyst, light oil conversion catalyst, medium temperature shift catalyst, high pressure methanol catalyst and low pressure methanol catalyst.3. Dyes, pigments and pigments Basic dyes, cadmium sulfide, ceramic color, chrome yellow, copper oxide, fast dyes, food color, indigo dyes, iron oxide, kaolin, zinc barium white, milolian, organic pigments, paints, phthalocyanine, titanium dioxide, watercolor, zinc chromite, potassium zinc chromite, zinc tetroxide chromite, reactive turquoise blue, carbide green B, whitening agent.4. Ceramics, Glass and Porcelain Alumina, bentonite, beryllium oxide, calcium carbide, silicon carbide, cement, electric porcelain, enamel, ferrite, floor tile material, glass sand, grinding wheel material, insulating material, iron oxide, kaolin, sand, silicon oxide, spark plug material, saponite, titanate, tungsten carbide, uranium oxide, wall tile material, zinc oxide, zirconium silicide.5. Carbohydrate-like products Corn wine, glucose, gum arabic, lactose, fructose, sorbitol, starch, sugar, wheat flour.6. Atractylodes, fungicides and insecticides Calcium arsenate, cupric chloride, cuprous oxide, 2,4-dichloro-phenoxyacetic acid, 2,4-dichloro-phenoxypropionic acid monomethylamine salt, dichloro-phenoxypropionic acid, dichloro-sodium propionate, lead arsenate, methyl-chloro-phenoxyacetic acid, methyl-chloro-phenoxyacetate, methyl-chloro-phenoxypropionic acid, sodium-aluminium-fluoride, sodium-methyl-arsenate, sodium-pentachlorophenol aldehyde, Thiophenol Chemical colloid, zinc-diethyl-dithiocarbamate, zinc-dimethyl-dithiocarbamate, herbicides, insecticides, fungicides.7. Dairy products and eggs Baby food, yogurt, casein, caseinate, cheese, sugar coconut juice, fresh cream, eggs: egg white, yolk, whole egg, ice cream mixture, milk substitutes, mixed dairy products, skim milk, whey, whey mother liquor, whole milk.8. Food and food extracts Artichoke, cake mixture, chrysanthemum tea, coconut mixture, coffee essence, substitute coffee essence, decaffeinated coffee essence, fat-containing flour mixture, condiment, blended juice, garlic, rose juice, liquorice extract, wheat essence, milk coffee mixture, Spanish toothed capsicum, vegetable protein, hydrolyzed protein, crude chymosin, soup mixture, tea essence, tomato, fungus Silk vitamin B12, nicotinic acid, protease, hydrolyzed protein, sorbitol, valerian, soluble fish meal, fish milk, fish protein.9. Pharmaceuticals and Biochemicals Aluminum hydroxide, sucrose sulfate, streptomycin sulfate, vitamin A, vitamin E, xanthothiazole, tetracycline, ampicillin, rutin derivatives, amoxicillin, oxytetracycline, penicillin, ampicillin, amylase, aspirin, serum, calcium lactate, calcium pantothenate, succinylchloramphenicol, dextran, fluoroo-chloropenicillin, Rhamnus peel, hormonal, dextran Ferric glucan, iron glucan, liquorice, heparin, L-lysine, magnesium hydroxide, vitamins, antibiotics, enzymes, dextrins, heparin, medium and extracts of Chinese herbal medicines.10. By-products, blood and fish products from slaughterhouses Animal Protein, Animal Blood, Dark Albumin, Light Albumin, Brain, Fish Albumin, Fish Meal, Fish Milk, Fish Sauce, Gum and Hydrolyzed Gum, Liver, Whale Dew11. Detergents and Surfactants Alkyl-imitated aluminates, detergents, dispersants, emulsifiers, fatty ethanol sulfate, heavy detergents, light detergents, potassium orthophosphate and potassium orthophosphate, calcium orthophosphate and dicalcium orthophosphate, nitrile triacetate, optical instrument brightener, phosphate ester, saponin, soap, tetrapotassium polyphosphate, synthetic laundry powder, sodium dodecanol sulfate and saponin.12. Organic Compounds Adipic acid, aluminium formate, aluminium hard ester, aminophenol disulfonate, aspirin, bismuth compound, calcium acetate, calcium butyrate, calcium gluconate, calcium lactate, calcium propionate, calcium gluconate, calcium stearate, cellulose acetate, CMC, methylmorphine phosphate, edetate, magnesium complex, glutamic acid, glycerin, glyoxal, lactose, lysine, malic acid, mercaptophiazole Suspension, metal stearate, oxalic acid, p-aminosalicylic acid, potassium phthalate, potassium sorbate, rubber catalyst, salicylic acid, sodium acetate, sodium benzoate, sodium dimethyldithiocarbamate, sodium ethyl xanthate, sodium carbonate, sorbite sodium, stearic acid, wax, zinc stearate.13. Inorganic Compounds Aluminum chloride, alumina, aluminium phosphate, aluminium silicate, aluminium sulfate, ammonium chloride, ammonium molybdate, ammonium nitrate, ammonium phosphate, ammonium sulfate, ANC catalyst, antimony sulfide, arsenic oxide, barium chloride, barium sulfate, bauxite waste liquid, bismuth carbonate, borax, boric acid, calcium carbonate, calcium chloride, calcium hydroxide, calcium phosphate, calcium propionate, calcium silicate, calcium sulfate, calcium sulfate, etc. Catalyst, cement (raw material), chromium dioxide, chromium sulfate, cobalt sulfide, copper oxychloride, copper sulfate, copper sulfide, cryolite, copper oxide, mortar flotation ore, graphite, iron oxide, kaolin, lithium chloride, zinc barium white, aluminum magnesium silicate, magnesium hydroxide, manganese carbonate, manganese oxide, molybdenum disulfide, nickel carbonate, nickel hydroxide, nickel sulfide, potassium bicarbonate, chloride, chlorine Potassium acid, magnesium peroxide, potassium nitrate, potassium permanganate, potassium persulfate, potassium phosphate, silica gel, sodium antimony, sodium bicarbonate, sodium dichromate, sodium chlorate, sodium chromate, sodium cyanide, sodium bisulfate, sodium hypochlorite, sodium phosphate, sodium silicate, sodium aluminosilicate, sodium fluosilicate, sodium sulfate, sodium trisulfate, thorium carbonate, titanium tetrachloride, uranium dichloride, zinc carbonate, sulphur Zinc acid.14. Mineral drying Such as copper concentrate, nickel concentrate, platinum concentrate, oxidized concentrate, aluminium concentrate, zinc concentrate, tin concentrate, precipitated copper, precipitated aluminium hydroxide, precipitated nickel carbonate, precious metal mud, bentonite, cryolite, kaolin and phosphate, etc.15. cellulose Mechanical pulping, other pulps, secondary fibers, semichemical and mechanochemical pulps, sulphates, sulphite waste liquor16. By-products and other materials Asphalt rubber, bentonite, coal, cork, diatomite, dregs, pressed coffee beans, yeast raw materials, corn gluten, plastic powder, pectin waste, seawater, sewage, sewage sediments, wheat gluten, wood flour.Two. Centrifugal spray dryer. Centrifugal spray dryer is equipped with centrifugal atomizer, hence its name. Centrifugal spray dryer is one of the most widely used Zui driers in industrial production. The liquid is centrifuged and thrown into droplets and dried in the dryer by adding liquid to the high speed rotating disks. On the surface of the disc, the liquid diffuses in a thin film shape and is thrown out at a high speed at the circumference. The atomization effect depends on the circumferential linear velocity and feeding rate, as well as some physical characteristics of the liquid. The characteristics of the centrifugal spray dryer are basically determined by the characteristics of the atomizer. (1) centrifugal spray drying does not require strict filtration equipment. If there is no fibrous liquid in the material, the material and liquid passages will not be blocked. 2. It can be used for high viscosity liquid (compared with pressure spray drying). (3) Because the speed of the atomizer is easy to adjust, it is easier to air the product size and narrow particle size distribution. (4) The same product can be obtained with the change of feed rate (+25%) without changing the working state of the atomizer when adjusting the throughput. _Because the fog group produced by centrifugal atomizer is basically on the same horizontal plane, and the fog droplets move along the radial and tangential direction of synthesis, there is almost no axial initial velocity, so the diameter of the dryer is relatively large. The diameter and length of the drying chamber are relatively small, and the space of the drying chamber can be utilized to a great extent by Zui.The centrifugal spray dryer has the following disadvantages: (1) The contact mode between droplets and gases basically belongs to the form of parallel flow, and the dispersing disc can not be placed vertically. (2) The processing accuracy of the dispersing disc is required to be high, and good dynamic balance performance is required. If the balance state is not good, the spindle and bearing are easy to be damaged. 3. The product stack density pressure spray drying is lower.(1) Atomization mechanism of centrifugal atomizer When a liquid is injected into a high-speed rotating dispersing disk, the liquid is accelerated to split and atomize under the action of centrifugal force and gravity. At the same time, at the interface between the liquid and the surrounding air, the existence of friction also promotes the formation of droplets. For this reason, the former is called centrifugal atomization, and centrifugal force plays a major role. The latter is called velocity atomization, and the centrifugal force only accelerates the liquid. The two kinds of atomization are introduced separately consciously in the study of atomization theory. In practice, it is difficult to distinguish the two kinds of atomization phenomena at the same time. When the feed rate is small and the rotating speed is low, the product size distribution produced by centrifugal atomization is narrower than that of pressure and airflow. Generally, the formation of droplets on the surface of a rotating dispersing disk depends on many conditions, such as the viscosity of the liquid, surface tension, inertia of the liquid on the dispersing disk, and the friction between the liquid and the air interface when it is released. The properties of liquid, especially the viscosity and surface tension, are the main factors of the dispersing disc at low rotating speed. In industrial production, the rotational speed of atomizer is often higher, and the inertia and friction are the main factors to form droplets. When the viscosity and surface tension of the feed are dominant, droplets will form separately and release from the edge of the dispersion disk to form uniform droplet clusters. Because of the strong internal force produced by the viscosity of the feed liquid, which prevents the liquid from breaking at the edge of the dispersing disc, it requires a large amount of energy to obtain a higher dispersion. Higher surface tension produces larger particles, which are produced in the thick liquid film at the edge of the dispersion disk. Lower surface tension lengthens the liquid wire and produces smaller droplets when it breaks. For high viscosity and high surface tension materials, spherical particles are usually produced, and droplet diameter can be easily controlled by changing operating conditions. The fog group produced by centrifugal nebulizer is basically on the same horizontal plane, unlike the other two nebulizers, which eject liquid at a certain angle. Centrifugal atomization can be basically summarized as three cases: material-liquid splitting into droplets directly, filamentous splitting into droplets and membrane splitting into droplets.1. Directly splitting material into droplets When the feed quantity is small, the feed liquid is moved to the edge of the dispersing disc by centrifugal force, and the hemispherical liquid ring rises around the dispersing disc. The shape depends on the viscosity, surface tension, centrifugal force and the shape and smoothness of the dispersing disc. When the centrifugal force is greater than the surface tension, the spherical droplets on the edge of the dispersing disc are thrown out immediately and atomized, accompanied by a small number of large droplets.2. Filamentous splitting into droplets The hemispherical liquid is drawn into many filamentous liquid lines when the flow rate of liquid is large and the rotating speed is accelerated. With the increase of flow rate, the number of liquid filaments around the dispersing disc is also increasing. If a certain amount is reached, the liquid filament will become thicker, and the number of liquid filaments will not increase, and the liquid filament thrown out is not stable. The fluctuation and inhomogeneity of the motion of the liquid filament breaks near the edge of the dispersing disc and shrinks into spherical shape under the action of surface tension.3. Membranous splitting into droplets When the flow rate of liquid continues to increase, the number of liquid filaments and the diameter of the filaments no longer increase, and the filaments adhere to each other to form thin films. When the liquid film is thrown out by centrifugal force at a certain distance around the dispersing disc, the liquid droplets are divided into dispersed droplets. If the rotating speed is further increased, the liquid film will shrink to the periphery of the dispersing disc and the liquid film band will narrow. If the sliding energy of the liquid on the surface of the dispersion plate is reduced to Zui small, the liquid can be ejected at high speed, and the atomization is split by friction with air around the dispersion plate. From the above analysis, it can be seen that the three atomization mechanisms may occur at different operation stages or at the same time, but there is always one main form of atomization. Which kind of atomization is the main factor is related to the shape, diameter, rotational speed, feed volume, surface tension and viscosity of the dispersing disc.(2) Structure of atomizer1. pneumatic type The main pneumatic driving mode is to install a turbine wheel on the spindle. The compressed air drives the turbine wheel to drive the spindle to rotate, so as to drive the atomization dispersion disk to rotate at high speed. The characteristics of this nebulizer are stepless speed change by adjusting the pressure and volume of compressed air, and there is almost no mechanical wear problem. The atomizer has simple structure and does not need to be repaired. The pressure of compressed air is between 0.2 and 1.0 MPa. It is mainly suitable for small experimental devices.2. Electromechanical Integration The electromechanical atomizer uses a high-speed motor to drive the dispersing disk directly, which eliminates the complicated mechanical transmission structure and reduces the mechanical wear. Moreover, the input power adjusts itself with the change of processing capacity. Therefore, the energy consumption of the atomizer is 50%-60% of the mechanical transmission, and 30% less than that of the pneumatic atomizer. The structure is to install the coil of the motor in the shell of the atomizer, and the dispersing disc is installed on the spindle of the motor. The speed of the spindle can be changed by adjusting the frequency of the motor, and the speed of the spindle can also be adjusted steplessly.3. Mechanical transmission There are two types of mechanical transmission, one is gear transmission, the other is belt transmission. Gear transmission is a motor driven big gear, the big gear meshes with the pinion of the spindle. The speed of the spindle varies with the transmission ratio of the gears. When the material input fluctuates, the speed of the spindle is constant and the mechanical efficiency is high. But the gear transmission structure will generate heat. The gear box needs lubrication and forced circulation cooling by oil pump, so the impact resistance of the equipment is weak. Belt drive is to drive large pulleys by motor, and then small pulleys on the spindle by belt. In theory, the speed ratio is equal to the inverse ratio of the diameter of large and small pulleys. The advantage of belt transmission is that the transmission system does not need cooling and lubrication, and has strong impact resistance. The disadvantage is that the spindle speed will fluctuate with the change of feed rate. For large mechanical transmission atomizer, because of the relationship between working environment, cooling system must be used to discharge heat from the atomizer due to mechanical transmission and drying process. At present, the main cooling methods are water cooling and air cooling. The structure of water cooling requires good airtightness and circulating water is pumped. Air cooling is forced cooling by ventilation through fans. One outlet enters the cold air, the other outlet discharges, the structure is relatively simple.(3) Type of Dispersing Disk of Atomizer The high-speed rotation of the dispersing disk also produces the following three functions: The pressure of the dispersing disc on the air; (2) The attraction formed by the friction between the surface of the dispersion disk and the air; The momentum transmitted to the air during atomization. As mentioned earlier, the basic principle of centrifugal atomizer is to drive the spindle, which drives the dispersing disc fixed on it to rotate at high speed. The main types of dispersing discs are rotor dispersing disc, multi-tube dispersing disc, linear airfoil dispersing disc and curve airfoil dispersing disc.1. Rotary Disperser The rotating cup dispersing plate, such as an inverted cup, has a smooth surface and sharp periphery. The feeding tube is set at the center, and the liquid first falls on the liquid distributor to make it flow downward uniformly along the cup body. When it reaches the cup mouth, the liquid is thrown out by centrifugal force and atomized. This structure is suitable for obtaining finer particles. It is mainly composed of feeding pipe, spindle, liquid distribution plate and rotary cup.2. Multi-tube Dispersible Disk A number of nozzles are evenly arranged on the dispersing disc. These nozzles are mostly made of wear-resistant materials, which can obtain a larger linear velocity when the rotating speed of the dispersing disc is not high. The size of the pore and the length of the extension can control the particle size of the product. At present, it is widely used in food drying.3. Linear Airfoil Dispersion Disk Linear airfoil dispersing disc distributes several liquid channels uniformly in the circumference of dispersing disc. The center line of channel mouth is a radial shape centered on dispersing disc. The channels are round, square and rectangular. The processing cost of the dispersing disc is low, and the material liquid is not easy to block the passage, but sometimes the passage can enter the air. In order to reduce the difficulty of processing, the dispersing discs are often processed separately and assembled again, and many straight lines are formed between the disks and the disks. This kind of structure is reasonable, and the sliding of material and liquid depends on the moving speed of liquid film on the disk. Closer to the center of the disk, the motion speed is not large, so the slip is not large. A channel is set at a certain distance from the center of the off-axis to prevent material-liquid sliding, increase the periphery of the wetting surface, and make the film move vertically along the channel. This structure can increase the throughput by changing the cross-section area of the channel without changing the diameter of the dispersion disk, and the fog spacing is basically the same. Some studies have shown that the smaller the cross-sectional area of the channel, the smaller the droplets produced, and vice versa, the larger the droplets produced.4. Curved Wing Dispersion Disk The basic structure of curved airfoil dispersion disk is basically the same as that of straight airfoil, but the channel of curved airfoil is curved groove. In this dispersion disk, it can be divided into high curve, low curve and hyperbola. Compared with the straight-line airfoil, the processing cost is slightly higher, but the bulk density of the product is about 7%-10% higher than that of the former. When choosing a centrifugal spray dryer, the choice of nebulizer type is very closely related to the drying effect. The performance difference of the nebulizer has been introduced before, so as to provide reference for selection. Centrifugal spray dryer flow chart 2-31.Three. Airflow spray dryer. Airstream spray drying is also one of the typical spray drying patterns. It is named after the airflow nebulizer (nozzle). The performance of the spray dryer and the shape of the main body of the dryer are mainly determined by the characteristics of the airflow nebulizer, which is mainly applied to the industries with fine grain size, such as medicine and other industries. The airflow spray dryer is smaller in diameter (compared with the other two dryers), especially for some materials with high viscosity and thixotropy. Gas-liquid two-phase contact is more flexible, and can be operated in parallel, mixed and countercurrent. However, due to the long spray distance of the airflow nebulizer, the height of the dryer should be lengthened appropriately to ensure that the droplets have enough residence time when the upper spray and lower parallel flow operation is adopted. Usually, the power consumption of air-flow atomizer is higher than that of the other two, usually 6-8 times of the other two. However, because it can atomize the material with high viscosity, which is inferior to other types of atomizers, it can also process the material with high solid content, reduce the energy consumption of drying, to a certain extent, make up for its shortcomings, so that the early model of Zui is still widely used in industrialization.(1) Airflow atomizer1. Working Principle of Airflow Atomizer The working principle of airflow nebulizer is to split liquid film by high-speed airflow. Compressed air or steam can be used in high-speed airflow, which is more economical than compressed air. The use of steam is limited by the material's heat-resistant temperature, so it can only be used when the material's heat-resistant temperature permits. When compressed air or steam is ejected from the atomizer at a high annular velocity (usually about 200 m/s, sometimes even at supersonic speed), the velocity of the feed liquid is very low, so there is a large relative velocity difference between the two, which results in friction and shear force between the gas and the liquid. The liquid is pulled into a thin filament in an instant, and then these filaments break quickly at a relatively fine point and form a tiny one. Droplets. The existence time of the filament depends on the relative velocity between gas and liquid and the physical properties of the material and liquid. The higher the relative speed is, the thinner the liquid filament is, the shorter the time and the higher the dispersity of the spray. The longer the filament exists, the greater the viscosity of the feed. For this reason, when the airflow spray drying process is used to treat some high viscosity liquid, the products obtained are usually powdery or flocculent, and the floc products are produced directly by liquid filament.2. Basic structure of airflow atomizer Airflow atomizer also has many structural forms, but no matter how it changes, the basic structure is unchanged. That is to say, atomizer is mainly composed of intake pipe, feed pipe, adjusting parts and gas disperser. In the atomizer, the adjusting part mainly adjusts the relative position between the end face of the trachea and the end face of the material pipe to adjust the mixing state of the gas and liquid phases. Gas disperser is to distribute the gas into the trachea evenly so as to ensure the uniform ejection at the exit of the trachea. In addition, the gas can also adjust the flow direction through the gas disperser, which can make the gas rotate to enhance the dispersion effect and drying process. Air-flow atomizer can be divided into two types according to gas-liquid mixing mode: internal mixing type and external mixing type. Internal mixing is the mixture of liquid and gas in the atomizer. The atomization process not only has the friction of gas, but also produces the dispersion of impact in the atomizer, so it saves more energy than external mixing. However, because the material liquid begins to disperse in the atomizer, if the operating temperature is higher, the atomizer is easily blocked by the solid formed by the dry powder, so it should be used cautiously in the drying operation. The difference between the external mixing air atomizer is that the material liquid and the atomized gas contact after ejection to disperse the material liquid. This operation is relatively stable. The airflow atomizer can be divided into two-flow, three-flow and four-flow according to the number of passages through which gas and liquid enter the atomizer. The second-flow type is gas-liquid type, that is, the outer tube takes the gas and the inner tube takes the liquid. The three-flow atomizer is two-gas-one-liquid type. The inner and outer tubes take gas and the middle takes liquid. In theory, the particle size of the three-flow atomizer is about 15% smaller than that of the two-flow atomizer. In addition, there are four-flow type, four-flow type and three-flow type are basically the same, but in the Zui inner layer there are additional air pipes, which take high temperature hot air flow, the purpose is to introduce heat to the center of the fog flame, in order to strengthen the heat transfer process. But this structure is seldom used, and the two-stream external mixing atomizer is mostly used in industry. The characteristics of airflow spray drying are simple structure, convenient processing, large operation flexibility and easy adjustment. But when installing, attention should be paid to the concentricity of atomizer and dryer, otherwise there will be wall sticking and other phenomena. The flow chart of airflow spray dryer is shown in figure 2-32.Four. Pressure spray dryer Pressure spray dryer (because of its high equipment and tower shape, also known as spray drying tower) is widely used in the production of Zui. The products of pressure spray dryer are particulates, and the average particle size can reach 150 ~ 200m. The product has good fluidity, wettability and other application performance, so it is welcomed by users. Pressure spray drying is mainly determined by the working principle of the pressure atomizer, so that the drying system has its own characteristics. Due to the particulate matter produced by pressure spray drying, the droplet drying time is longer for both droplets and products than for the other two types. In addition, the spray angle is also small, generally between 20 ~70, so the shape of the dryer is mainly high tower, so that the droplets can have enough residence time. The feeding liquid is atomized by atomizer under certain pressure, so there must be a high-pressure pump in the system. In addition, because the atomizer aperture is very small, in order to prevent impurities from blocking the atomizer aperture, it is necessary to filter the material before entering the high-pressure pump. Pressure spray drying is mostly used to obtain granular products. Therefore, the Zui end products produced by pressure spray drying have their unique application properties. Pressure atomizers (some monographs are called pressure nozzles) are important components of pressure spray dryer. Pressure atomizers are also called single fluid atomizers or mechanical nebulizers in some documents. The atomization mechanism is that the liquid enters the rotating chamber at high speed from the tangential passage of the atomizer under the pressure of the high-pressure pump, which makes the liquid rotate at high speed in the rotating chamber. According to the conservation law of moment of momentum, the rotating speed is inversely proportional to the radius of the rotating chamber, so the closer the rotating speed is to the axis, the smaller the static pressure is. When the rotating speed reaches a certain value, the pressure at the center of the atomizer equals the atmospheric pressure, and the liquid ejected forms a conical annular liquid film revolving around the air center. With the prolongation of the liquid film, the wave formed by the violent disturbance of air continues to develop, and the liquid film splits into thin lines. Affected by the radial partial velocity of turbulence and the relative velocity of ambient air, the liquid film breaks into filaments after zui. After breaking, the liquid filament is subjected to the action of surface tension. After zui, a mist group composed of numerous droplets is formed. After evaporation of water, a particulate product is formed. Over the years, many drying experts at home and abroad have done a lot of research work on the structure of pressure atomizer, and many structural forms have been developed. The common characteristic of pressure nebulizer is that liquid enters the nebulizer at high pressure and rotates at high speed. After obtaining enough centrifugal force, it sprays out from the nebulizer hole. Because of its many structures, in order to design and use conveniently, the pressure atomizer is divided into two categories: rotary pressure atomizer and centrifugal pressure atomizer. These two types of atomizers can make the liquid rotate inside the atomizer, but the structure of rotation is different.Pressure spray drying also has its own disadvantages. Flow rate can not be adjusted in the production process. The flow rate mainly depends on the orifice diameter and operating pressure of the atomizer outlet, and the change of operating pressure will affect the particle size of the product. Therefore, if you want to change the flow rate, only change the orifice of the atomizer or adjust the operating pressure. 2. Pressure spray drying is not suitable for dealing with fibrous or granular materials. These materials are easy to clog the nebulizer passages. (3) It is not suitable for treating high viscosity materials or suspensions with solid-liquid interface, which will cause serious uneven product content. 4. Compared with the other two types, the volume evaporation intensity of pressure spray drying is lower. In related content, we have introduced raw products produced by spray drying, but the pressure spray drying granulation technology mentioned here has been applied to the following products. Chemical industry: catalyst, resin, synthetic laundry powder, grease, ammonium sulfate, dyes, dye intermediates, white carbon black, graphite, ammonium sulfate, pesticides, potassium fluoride, whitening agent CXT. Foods: amino acids, condiments, protein, starch, dairy products, coffee extract oil, full-fat milk powder, prion, cocoa milk powder, milk powder, egg white (yellow), oats, chicken juice, instant tea, spice meat, protein, soybean, peanut protein, corn syrup, corn starch, glucose, pectin, maltose, potassium sorbate, pumpkin powder. Fish meal, meat powder. Drugs: Chinese patent medicine, antibiotics, Chinese medicine granules, Chinese medicine extracts, glue, yeast, vitamins, antibiotics, amylase, lipase. Ceramics: Magnesium oxide, porcelain clay, various metal oxides, dolomite, kaolin, alumina, talc. Plastics: ABS emulsion, urea formaldehyde resin, rubber (urea) formaldehyde resin, polyethylene, polyvinyl chloride.